What Is The Difference Between Solder Flux And Solder Paste?
Solder paste is used when assembling components while the solder flux is used before applying the solder paste. So they are different from each other in the components as well as the time of application.
So in this article, you will find everything you need to know about the solder paste and the solder flux, and finally, we differentiate those two for a better understanding. So we invite you to stick around until the end, and this is RLC Talk.
What is solder paste?

Solder flux and petroleum jelly are combined to create solder paste grease. It is advantageous because when heated by the soldering iron, it “sticks” to objects and spreads out around the area being soldered. It is simpler to apply solder flux evenly to the entire soldering area when solder paste grease is used.
How do you make solder paste?
A metal alloy powder (about 90% by weight) and a cream-like substance made of organic chemicals (about 10% by weight) are combined to create solder paste. The “flux” organic chemical cream is typically protected by patents and/or trade secrets.
What is the paste for when soldering?
Metal solder particles and a putty-like flux are combined to form a solder paste, which has the consistency of a powder.
The flux serves as a temporary adhesive to hold the surface mount components in place in addition to performing its regular function of cleaning the soldering surfaces of impurities and oxidation.
What are the grades of the solder paste?
Solder paste comes in a variety of grades, and the right one can be chosen depending on the PCB assembly method being used.
The small solder balls are used to classify the solder paste. The various types have a range of solder ball sizes between which 80% of the tiny solder balls fall because they cannot be precisely graded.
Can you use solder paste to join wires?
Solder paste is a reasonably good electricity conductor. It permits the assembly of PCBs and the joining of electrical wires with solder paste. Solder paste makes an electrical connection between them in addition to a mechanical one.
So, yes. You can use solder paste to join wires because it conducts electricity well, and also it acts as a good adhesive.
How long does solder paste last?
When refrigerated, solder paste typically has a shelf life of six months. One might wonder what would happen if the paste was chilled for two months, then thawed to room temperature, left there for 12 hours, and then refrigerated again.
How many types of solder paste are there?
There are basically three types of solder paste in use, and the following are those three kinds od pastes.
Flux core solder paste: Flux core solder is offered for purchase as a spool of “wire” that contains a reducing agent at the center. In order to create a cleaner electrical connection, the flux is released during soldering and reduces (reverses oxidation of) metal at the point of contact.
Additionally, it enhances the solder’s wetting characteristics. Rosin is commonly used as flux in electronics. Acid cores should not be used on electronics; they are intended for plumbing and metal repair.
Lead-free solder paste: When the EU started limiting the use of lead in consumer electronics, lead-free solder really took off. Manufacturers using lead-free soldiers may be eligible for tax benefits in the US.
Utilizing more recent annealing methods, adding additives like nickel, and applying conformal coatings can all help reduce tin whiskers. Lead-free solders typically have a melting point that is higher than regular solders.
Lead-based solder paste: It was lead-based solder that started the modern electronics era. The most typical mixture has a melting point between 180 and 190 °C and is a 60/40 (tin/lead) blend.
Tin, also referred to as soft solder, is chosen because it has a lower melting point than lead, which prevents the development of tin whiskers. The tensile and shear strengths improve with increasing tin concentration.
What is solder flux?
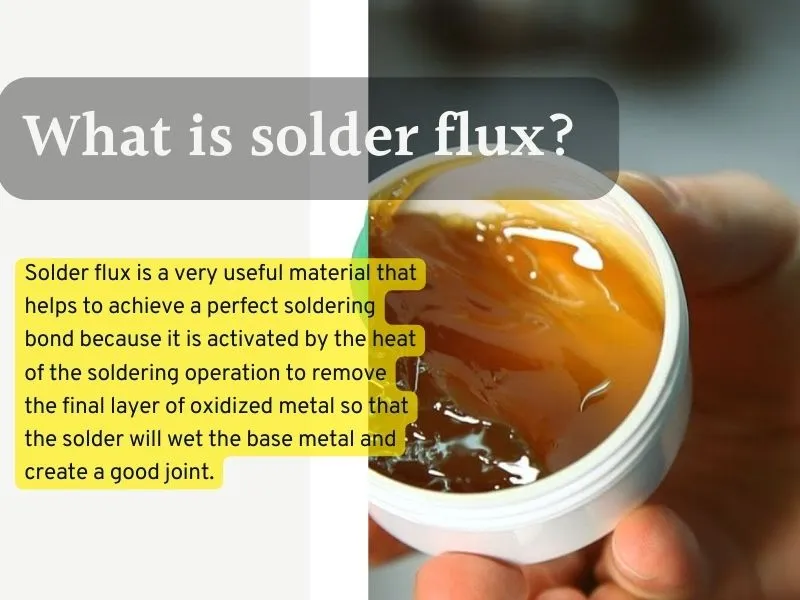
It is used in both automatic PCB assembly and hand soldering and is primarily used to clean the surface of the PCB before the soldering process.
Solder flux is a very useful material that helps to achieve a perfect soldering bond because it is activated by the heat of the soldering operation to remove the final layer of oxidized metal so that the solder will wet the base metal and create a good joint.
Compliance: Since they all offer similar uses, you can generally use any soldering flux for your electronics projects. However, purchasing something like a RoHS-compliant soldering flux can be a great idea if you want to ensure that your soldering flux has been properly tested.
Weight: Since soldering flux is something that is frequently used, you will need a lot of it. Therefore, be sure to verify the amount or weight of soldering flux that you are purchasing. Soldering flux typically comes in packs of 2 oz, though some brands also offer 4 oz or 16 oz packs for extended use.
Warranty: Because soldering flux is essentially a chemical mixture, it typically has a long shelf life. However, since you want your soldering flux to last as long as possible, it makes a lot of sense to look into the warranty that is offered by it. Fortunately, a lot of the soldering flux on the market comes with a one-year warranty.
Does Vaseline work as flux?
Yes, Vaseline functions just as well as brand-name flux, and you can even purchase a generic version.
Wax and mineral oils make up the majority of petroleum jelly’s composition, which prevents corrosion of your components.
Additionally, it removes metal oxides and cleans up the gunk that might jeopardize your bond.
What can I use instead of flux?
Petroleum jelly is the best substitute for flux because it is affordable, efficient, readily available, and has cleaning capabilities.
Lemon juice, homemade pine tar flux, and homemade rosin flux are other excellent substitutes.
Is solder paste the same as flux?
No, the solder paste and the solder flux are not the same, and they have different properties and different purposes from each other.
Flux is applied prior to assembly to help your board through the soldering process while the solder paste is used to assemble components onto your circuit board.
Some related FAQs.
Which is better liquid or paste flux?
What temperature does solder paste melt?
How long does solder take to dry?
1/4 Vs 1/2 Watt Resistor: Which One Is Better For Your Project?
RLC Talk