Maximizing Conductivity: The Importance of Solder-Coated Wire Conductors
Are you tired of dealing with poor conductivity and unreliable wire conductors in your electrical and electronic systems?
There is a simple solution that can help improve the performance of your wire conductors: coating them with solder.
Not only does solder coating increase conductivity and reduce resistance, it also increases the durability and reliability of wire conductors.
Keep reading to learn more about the benefits of solder coated wire conductors and how they are made to ensure consistent and effective coating.
The Benefits of Solder Coated Wire Conductors
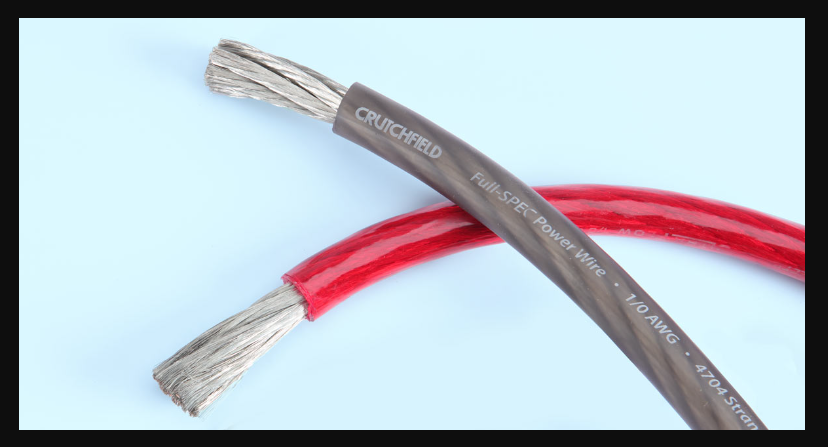
You might be wondering what makes solder coated wire conductors so special. Here are a few key benefits to consider:
Improved conductivity and reduced resistance: When wire conductors are coated with solder, the resulting layer of metal helps to improve the flow of electricity and reduce resistance. This can lead to better performance and more efficient use of energy in electronic and electrical systems.
Increased reliability and durability: Solder coating provides an extra layer of protection for wire conductors, helping to increase their lifespan and reduce the risk of failure. This can be especially important in applications where wire conductors are exposed to harsh environments or high levels of stress.
Ease of use and versatility: Solder coated wire conductors are easy to work with and can be used in a wide range of applications. Whether you need to connect components in an electronic circuit or splice together two wires, solder coated wire conductors can provide a reliable and secure connection.
Overall, the benefits of solder coated wire conductors make them a smart choice for anyone looking to improve the performance and reliability of their electrical and electronic systems.
How Solder Coated Wire Conductors are Made?
So, how exactly are solder coated wire conductors made? The process begins by cleaning the wire conductors to remove any dirt, oil, or other contaminants that could affect the quality of the solder coating.
Next, the wire conductors are heated to a high temperature using a soldering iron or other heating tool. This melts the solder, which is then applied to the wire conductors to create a thin, even layer of metal. The wire conductors are then cooled to solidify the solder coating.
It’s important to ensure that the soldering process is performed properly in order to achieve a high-quality solder coating. This includes using the right soldering iron temperature, applying the solder evenly, and allowing the wire conductors to cool properly.
Quality control measures are also important to ensure consistent and effective solder coating. This may involve testing the wire conductors for proper conductivity and resistance, as well as visually inspecting the coating for any defects.
By following these steps and using the right tools and techniques, it’s possible to create reliable, high-quality solder coated wire conductors that are ready to be used in a variety of applications.
Applications of Solder Coated Wire Conductors
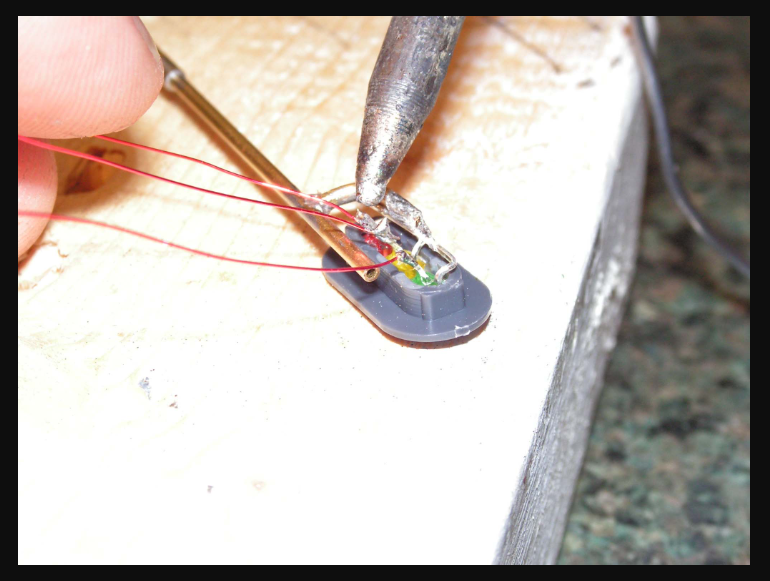
Solder coated wire conductors have a wide range of applications in the electronic and electrical industries. Some common examples include:
Electronic and electrical systems: Solder coated wire conductors can be used to connect components in electronic circuits, such as circuit boards, sensors, and motors. The improved conductivity and reliability of solder coated wire conductors make them ideal for use in these systems.
Automotive and aerospace industries: The high performance and durability of solder coated wire conductors make them well-suited for use in the automotive and aerospace industries. They can be used to connect various components in vehicles, as well as in aircraft systems.
Medical and military equipment: The reliability and performance of solder coated wire conductors make them a valuable choice for use in medical and military equipment. They can be used in a variety of applications, such as connecting sensors and monitors, as well as in communications systems.
The versatility of solder coated wire conductors makes them an important component in a wide range of industries and applications. Whether you need to connect components in an electronic circuit or splice together wires in a harsh environment, solder coated wire conductors can provide a reliable and effective solution.
Automated Optical Inspection for Quality Control in Manufacturing
rlc talk
Solder Coated Wire Conductors vs. Other Types of Wire Conductor Coatings
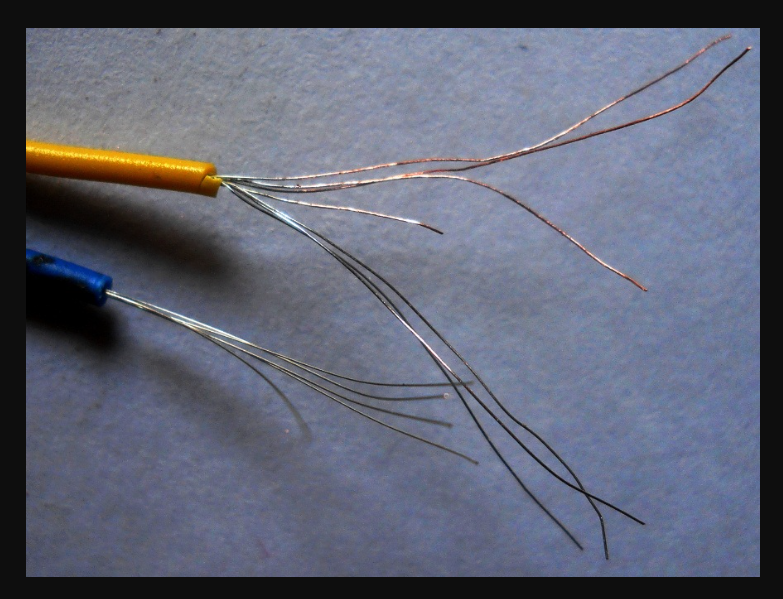
When it comes to improving the performance and reliability of wire conductors, solder coating is not the only option. There are several other types of coatings that can be used on wire conductors, each with its own set of benefits and drawbacks. Here’s a comparison of solder coated wire conductors versus some other common types of wire conductor coatings:
Plastic coatings: Plastic coatings can provide insulation and protection for wire conductors, but they do not offer the same level of conductivity as solder. Plastic coatings are generally best suited for applications where insulation is the primary concern, rather than improved conductivity.
Tin coatings: Tin coatings are similar to solder coatings in that they are both metallic and can improve conductivity. However, tin coatings may not be as durable as solder coatings and may be more prone to corrosion.
Silver coatings: Silver is a highly conductive metal, and silver coatings can provide excellent conductivity for wire conductors. However, silver is also a relatively expensive metal, and silver coatings may not be practical for all applications.
In general, solder coated wire conductors offer a good balance of conductivity, durability, and affordability. While other types of coatings may be suitable for certain applications, solder coated wire conductors are often the best overall choice for improving the performance and reliability of wire conductors.
Solder coated wire conductors offer a simple and effective solution for improving the performance and reliability of electronic and electrical systems. The improved conductivity and reduced resistance of solder coated wire conductors can lead to better performance and more efficient use of energy.
Additionally, the increased durability and reliability of solder coated wire conductors make them a valuable choice for use in a wide range of industries and applications. From automotive and aerospace to medical and military equipment, solder coated wire conductors are an important component in many different systems.
How to Troubleshoot Component Placement Issues in Altium?
rlc talk