Why Is The Suitable Solder Mask So Essential? Solder Mask Materials.
The solder mask is one of the most critical considerations for circuit boards. The solder mask is a protective layer covering the exposed copper on a circuit board. It serves two primary purposes: to prevent shorts between conductors and to protect the copper from oxidation.
There are two main solder masks: epoxy liquid and dry film. The epoxy liquid is the most common type of solder mask and is ideal for most applications. On the other hand, dry film solder masks are typically used in more specialized applications where reliability is critical, such as in military or aerospace applications.
The most popular color for solder masks is green, but other colors are also available. When choosing a solder mask for your circuit board, it’s essential to consider the application and select a material that will meet your needs.
Types of Solder Masks
There are four types of solder masks. The epoxy liquid is the most common type of solder mask and is ideal for most applications.
However, dry film solder masks are typically used in more specialized applications where reliability is critical, such as in military or aerospace applications.
Epoxy Liquid Solder Mask

Epoxy liquid solder masks are made from a photosensitive polymer cured using ultraviolet light. They offer excellent adhesion to the substrate and can be easily repaired if necessary.
In addition, epoxy liquid solder masks are typically less expensive than dry film ones, making them a good choice for budget-conscious projects.
Dry Film Solder Mask

Dry film solder masks are made from a heat-sensitive polymer cured using infrared light. They offer superior yields and uniformity compared to epoxy liquid solder masks, making them the preferred choice for high-volume production runs. However, dry film Solder masks can be more challenging to repair if necessary.
Polyimide-Based Solder Mask
A polyimide-based solder mask is made from either solution-coated polyimide or dry film laminate. This solder mask offers high-temperature Resistance because its glass transition temperature is generally above 260°C. It also has good dimensional stability characteristics.
Some disadvantages to using this solder mask are that it can be more expensive than other types and has poorer adhesion to certain metals like aluminum. Additionally, it can be yellowed by exposure to UV light over time. On the other hand, some advantages include that it offers halogen-free options and choices for RoHS compliance.
Additionally, it cures quickly at temperatures around 125°C – 150°C. And finally, it offers good flexibility compared to other types of solder masks.
Liquid Photoimageable Solder Mask (LPISM)
Liquid Photoimageable Solder Mask (LPISM) is a solder mask applied in liquid form and then cured using ultraviolet light. LPISM provides several benefits over traditional dry-film solder masks, including creating sharper features and finer line widths.
In addition, LPISM can be applied to both sides of a circuit board concurrently, which helps to speed up the manufacturing process. LPISM also has excellent adhesion properties, which helps to prevent component drift during soldering.
Overall, LPISM is an excellent choice for military and aerospace applications where precise soldering is essential.
Dry Film Photoimageable Solder Mask (DFSM)
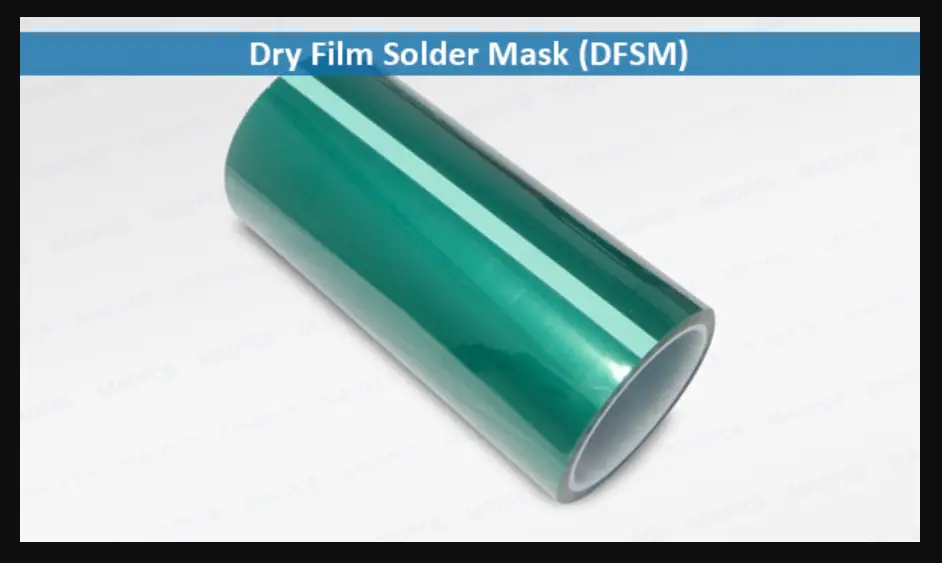
Dry film photoimageable solder mask (DFSM) is a material used to protect the exposed areas of printed circuit boards (PCBs) from corrosion and short circuits. It is a photosensitive film applied to the PCB and then cured with UV light.
The film can be printed or laminated onto the PCB. DFSM has many advantages over other solder masks, including its high durability, chemical resistance, and thermal stability.
It is also easier to apply and remove than other solder masks. However, DFSM is more expensive than different solder masks and can be challenging to work with.
Solder Mask Colors.
The most popular color for soldier masks is green, but various other colors are available depending on the application. Different popular colors include white, black, and red.
When choosing a color for your soldier mask, it’s essential to consider the contrast with the underlying circuitry. For example, if you’re using white circuitry on a green background, you’ll want to use a green soldier mask so that the circuitry is visible.
Whether you’re building a prototype or mass producing a commercial product, choosing the right type of soldier mask for your project is essential.
Epoxy liquid soldier masks are an excellent choice for most applications due to their low cost and easy repairability. However, dry film soldier masks may be better if you need superior yields and uniformity.
And finally, consider the contrast with the underlying circuitry when choosing a color for your soldier mask. With careful consideration, you can ensure that your project turns out just how you envisioned it.
How To Import Gerber Files In EasyEDA?
rlc talk
The application process of solder
Applying solder to a circuit board is a critical step in the manufacturing process. The solder helps to create electrical connections between the different components on the board. There are two main types of solder: lead-based and lead-free. Each type has its own advantages and disadvantages.
Lead-based solder is more expensive, but it melts at a lower temperature, saving time and energy during manufacturing. On the other hand, lead-free solder is less costly but requires more heat to melt, which can increase the risk of damage to components.
The solder application process involves first applying the solder material on the board and then following it up with making openings in the material for the copper components.
To ensure reliable electrical connections, it is vital to use the correct amount of solder and to apply even pressure when making connections. Too much or too little pressure can cause problems with the electrical connection.
rlc talk